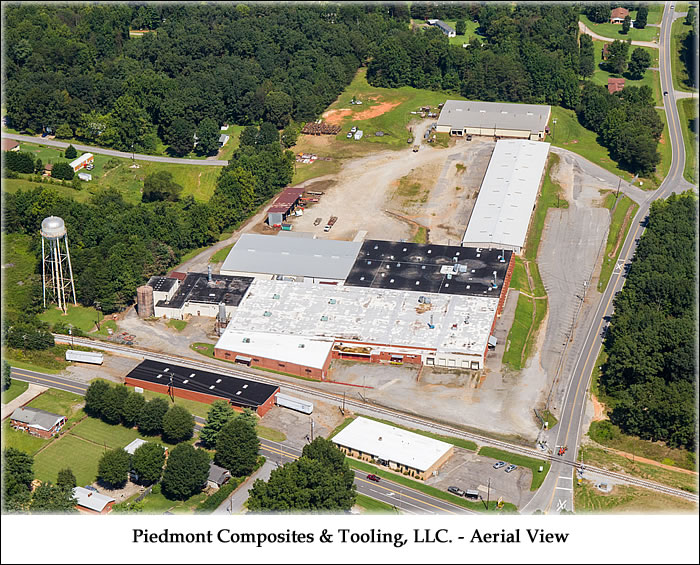
Listed below are the various departments in our
170,000 square foot factory located in Taylorsville, NC.
|
|
Open Molding
The Open Molding Department features 4 chopper guns that are supplied by a 53,000 gallon bulk resin system. Other features are a back coating system and a hand lay up station. A state-of the-art heated and cooled ventilation system ensures that a <50 ppm styrene level is maintained.
|
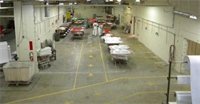 |
Light Resin Transfer Molding (LRTM)
A fully looped vacuum system features over 100 mold stations. A specifically designed resin flow system delivers precise amounts of resin to each mold.
|
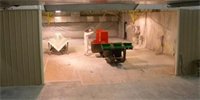 |
Gel-Coat
Our Gel-Coat Department features a temperature controlled storage and pump room. The gel-coat is sprayed via 8 color pumps and 2 gun booms. A computer controlled, heated and cooled ventilation system ensures that a >50 ppm styrene level is maintained.
|
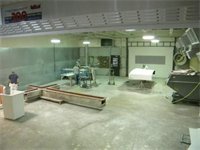 |
Trim Department
This department is a fully enclosed positive pressure environment. A computer controlled re-circulating filtered ventilation system ensures that no dust is directly discharged into the environment.
|
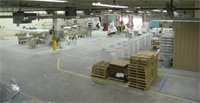 |
Finishing Department
Our Finishing Department is easily adaptable to several product lines. A step- by-step process line is used versus the traditional work booth process.
|
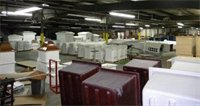 |
Shipping/Receiving/Warehouse
Finished products are stored indoors until they are ready for shipment.
|
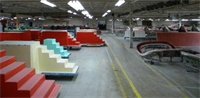 |
Tooling Storage
All of our molds that are not currently in production are stored indoors. This climate- controlled environment ensures that the life of the mold is not reduced by exposure to extreme heat or cold as well as U.V. damage.
|
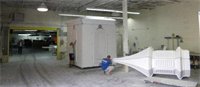 |
Custom/Tooling Department
From small molds to large architectural projects, this department is where most of the hand fitting and detail work is completed.
|